Choosing Material For a Metal Stamped Part
Looking for the right material for your stamped part?
Choosing the right material can be just as difficult as designing your custom part. There are so many elements to consider with materials and the wrong choice can make a huge impact on the functionality of your part. Imagine a clip that doesn’t snap back into place or an electrical contact that doesn’t conduct electricity well. The design of the part seems often like it’s only half the battle as you often have to make sure your material choice allows the functionality of the design to perform correctly. We have seen many cases where the design was perfect but with the wrong material choice the part failed and they redesigned the part rather than going with a new material that could have fixed the problem. This is why here at Gemco we always try to ask as much about the functionality of the part as possible because we can offer suggestions of the right material fit as well.
The various processes used in metal stamping and wire forming can transform flat metal and wire into an infinite variety of shapes. Your choice of material should all be based on your application and performance requirements of the specific components, as well as manufacturability.
When choosing a material, it’s important to keep the component’s application and the environment in mind. I like to ask myself some of these basic questions to hone in on which materials would be the best choice: Is it going to be exposed to extreme temperatures? Lots of humidity causing rust? Going to be exposed to saltwater? Or rain? Is weight a concern? Is aesthetics important? Do you want it to have a spring-like characteristic? Or do you need it not to bend at all? And, one of the most important questions, what’s my budget?
What material is right for you? Consider these common options:
Steel (Density: 0.28lbs./cubic inch)

Steel is easily one of the most common and versatile materials for virtually any type of industrial application. Its immense strength allows it to be used in environments where other metals would never be suitable. It’s also inexpensive, allowing you to control costs while still ensuring quality. The main drawback of steel is the potential for oxidation and rust. If this is a concern, consider using stainless steel, which contains chromium, to better resist tarnishing.
According to the American Iron and Steel Institute (AISI), steel can be broadly categorized into four groups based on their chemical compositions:
- Carbon Steels
- Alloy Steels
- Stainless Steels
- Tool Steels
Copper (Density: 0.30 lbs./ cubic inch)
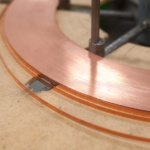
Copper is used to make parts combining exceptional conductivity with low cost. Both thermally and electrically conductive, copper can easily be used to achieve an 85% to 95% IACS rating. With advanced densification, electrical conductivity can be raised further to 100% IACS. Copper is a popular alternative to many high-priced conductors – and, when used correctly, performs as well or better. Copper changes color over time, but it is highly resistant to corrosion.
Aluminum (Density: 0.11 lbs/cubic inch)
Aluminum is a relatively soft metal used in a wide range of applications because of its cost-effectiveness. It is the material of choice for components that don’t need
to be unusually strong or conductive. Aluminum is one of the most common metals in the Earth’s crust and holds a similar status in manufacturing. In addition to being light and inexpensive, it’s also highly resistant to corrosion without any unusual treatment.
Phosphor Bronze (Density: 0.32 lbs./cubic inch)
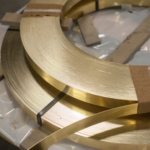
Bronze, an alloy of copper and tin, has been used since ancient times. Today, phosphorus can be added to bronze to further increase its toughness. Phosphor bronze provides greater strength than ordinary bronze at a comparable cost. It also retains all the many advantages of bronze: It is resistant to corrosion, withstands high temperatures with ease, and wears well against steel. It can be welded, machined, brazed, or soldered. Phosphor Bronze is often used for its spring characteristics.
Conclusion
Material selection is a crucial decision that involves balancing many competing factors. Cost, availability, and physical properties will influence every decision about what the right material is for your project. For expert advice, including which of our dozens of materials may be right for you, just contact the experts at GEMCO Manufacturing. We look forward to helping you make your latest project a reality!
Sources:
https://en.wikipedia.org/wiki/Steelmaking
http://www.essentialchemicalindustry.org/metals/iron.html
https://www.britannica.com/science/aluminum
Author: Annmarie Johnson